in Portugal
靴づくりを支える
テクノロジーと
クラフツマンシップ。
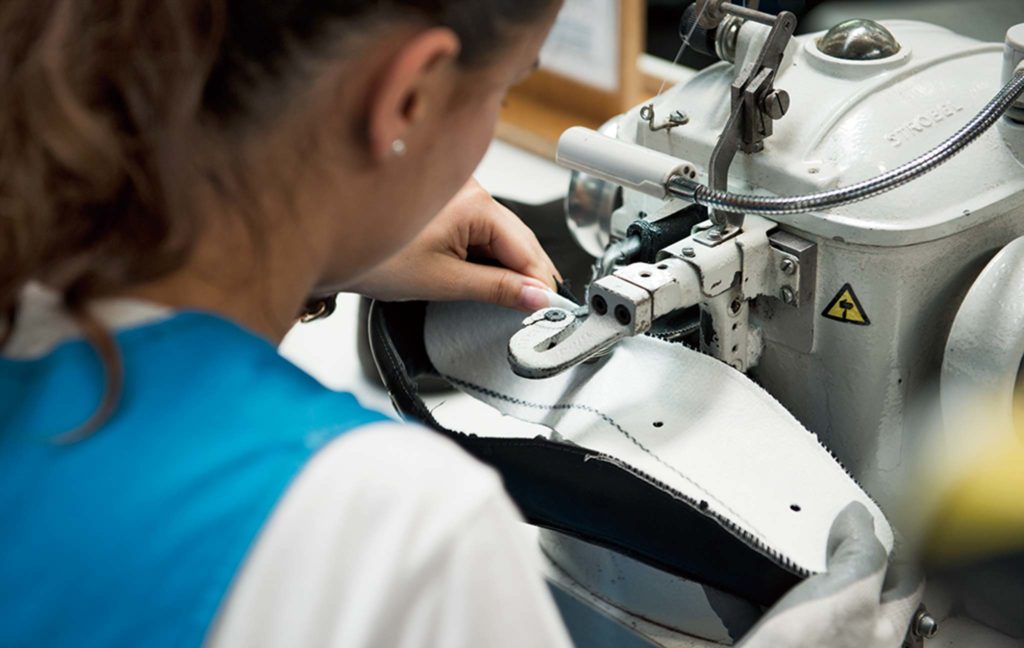
エコーは全世界に6つの靴工場を展開し、年間で2千万足を生産している。中でもポルトガルのファクトリーはエコー本社との関係が緊密で、デザイナーとともに商品づくりを行うR&Dの機能を担う一方、高度な技術を要するプロダクトを数多く手がけている。
「工場全体では1300名が働いていますが、R&D部門にはそのうち230名が従事しています」
エコー・ポルトガルの工場長、グスタボ・クレマー氏の言葉通り、先のエコー・レザー同様、工場内に工場全体の機能を凝縮したようなR&Dセクションがある。そこで行われているのは、プロトタイプやサンプルをつくる作業。デザインから各種パターンや金型のベースとなるデータをつくり、アッパーの縫製、フルイドフォルム製法による底付けまで、靴づくりがひと通り行われている。そして、大量に靴を生産するための準備段階として、さまざまな工程も含めて靴をめぐる「ストーリー」がそこでクリエイトされるのだ。
取材時にちょうどドレスシューズの最新モデル「ヴィトラス アーティザン」のセールスサンプルがつくられていた。フルイドフォルム製法の底付けでは、デンマークで見たパーツがヒールのパーツとともに金型上に置かれ、そこに木型が入ったアッパーが乗る格好で両側の金属が閉じ、PUが充填される。その間約180秒。その後PUを安定させるためにクールダウンさせる工程が必要だが、ごく短時間でソールが、靴の大半が出来上がる。
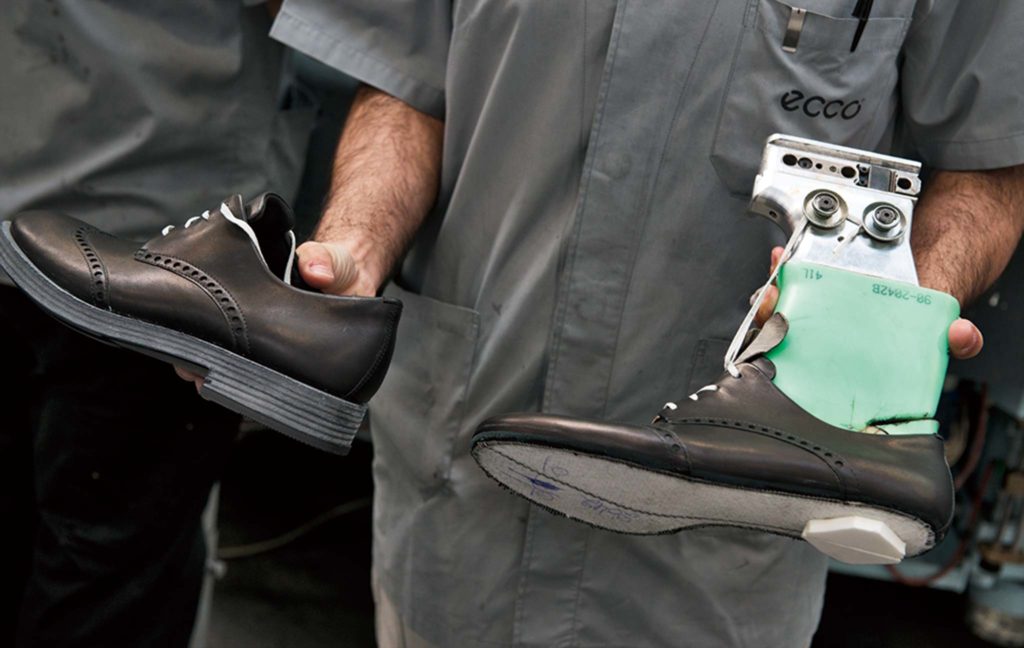
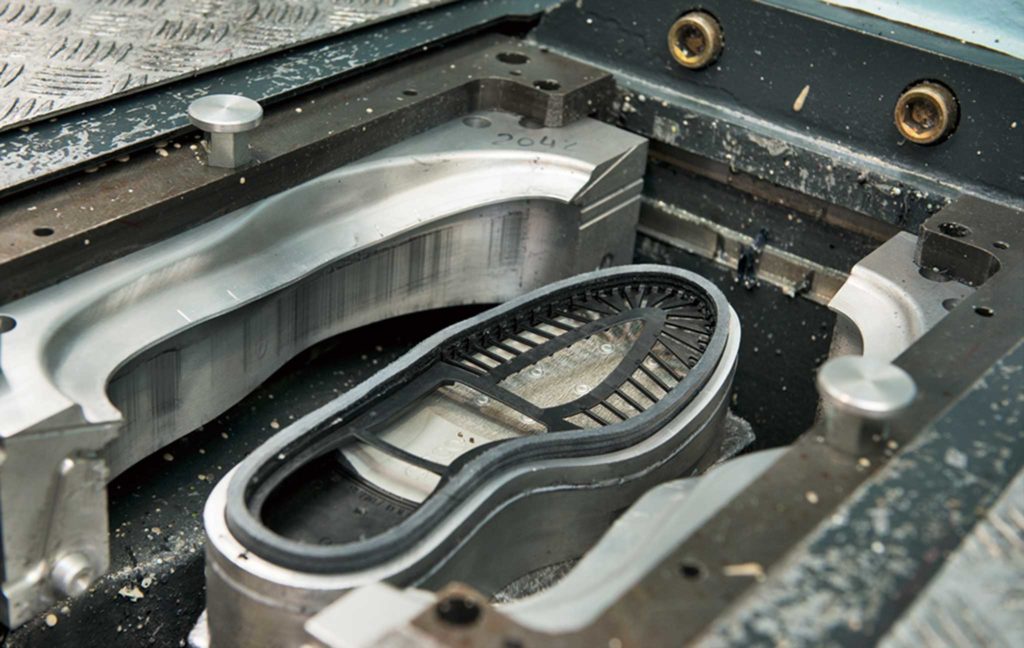
右/金型が開いて靴が表れた様子。枠の内側にはPUが充填され、アッパーと一体化している。この後革の枠は丸コバに加工される。
だが、このR&Dの後で案内された木型や金型づくりの現場で、エコーの靴づくりの深みを思い知らされた。ソールや各種パーツなどの成型に使われる金型は自社内でアルミニウムの塊から削り出される。コンピューターと連動した機械で大枠がつくられるものの、最終的には手作業で仕上げるという。1ペアの靴に対して必要な金型は6つ。展開モデルやサイズ数、求められる作業精度を鑑みると、フルイドフォルム製法の一瞬の背後には、膨大な時間とテクノロジー、そしてクラフツマンシップが存在していることがわかる。
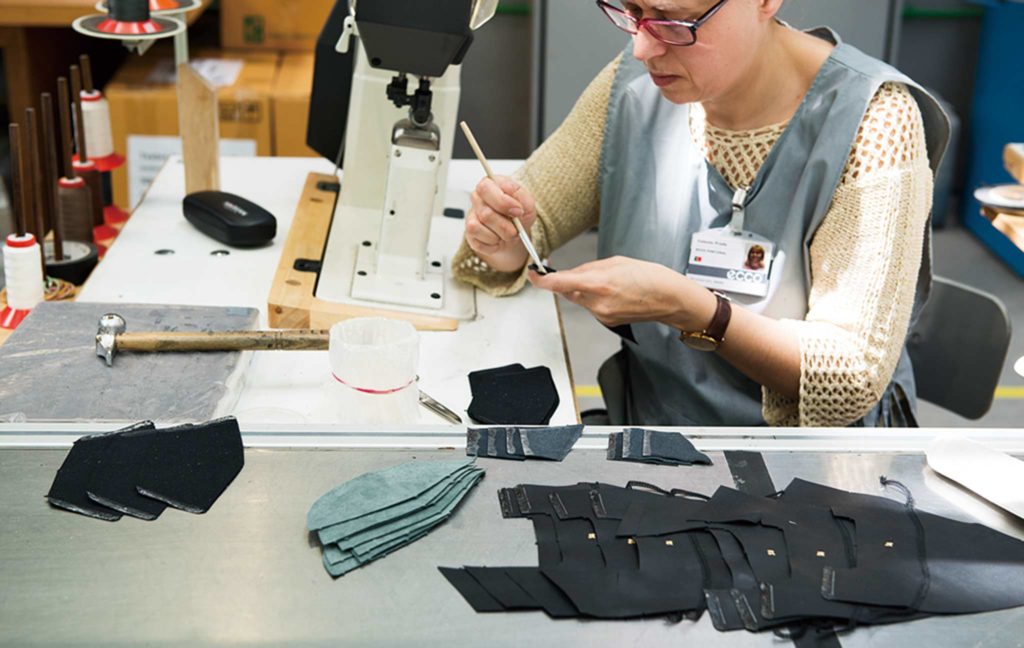
取材終盤、プロダクションの最終工程で、話題のモデル「エキソストライク」ほか複数の靴がランダムにチェックを待っているのを見た。一見非効率に見えるその様子はまた、多品種をものともしないファクトリーのポテンシャルが端的に表れているように思えたのだった。
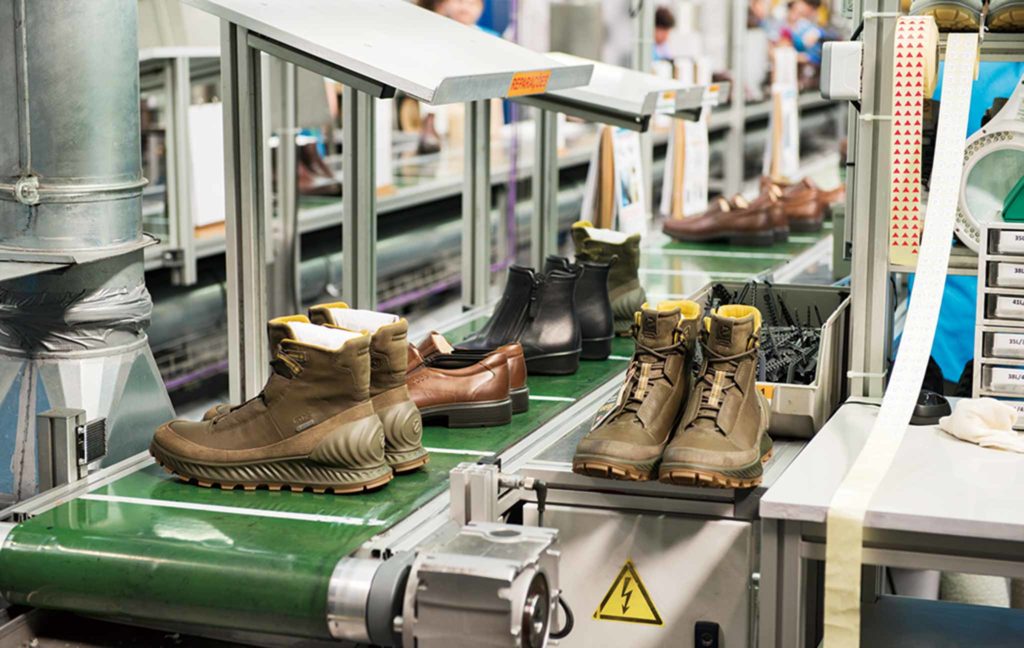
photographs_Satoko Imazu
text_Yukihiro Sugawara
○雑誌『LAST』 vol.15 「ECCO 革から靴まで、進化を続けるものづくりの現場。」より抜粋。