『スコッチグレイン』の靴づくり。その根底にあるのは、グッドイヤーウェルテッドに関する独自の探求だった。
2階ではつり込みからウェルティング(すくい縫い)、そして底付けまでが一気に行われている。旧工場の建物と新しいビルが繋がったことで、ワンフロアで作業が流れるようになった。先ほどの裁断の工程とは対照的に、ここには最新鋭の機械が数多く導入されている。
「新しいトウラスターやソールに圧力をかけるローラーなどの導入で、より木型形状を反映させた靴ができるようになりました」と廣川社長。従来からライニングにパンチングを配して通気性や伸縮性をもたせたり、コルクの代わりに合成樹脂のスポンジをフィラー(中物)に採用してクッション性と耐久性を強化するなど、『スコッチグレイン』のつくりには独自の合理性が盛り込まれていたが、それはさらに進化しているように見える。
もっとも、こうした同社の独自性は、単なる合理化というより、伝統的なグッドイヤーウェルテッドの靴のポテンシャルを最大限引き出そうとする姿勢から導かれたもの、といえるかもしれない。その姿勢は3階で行われていた、同ブランド独自の仕上げ「モルトドレッシング」の工程にも見て取れた。
「いまは新型コロナウイルスの影響から生産数を抑えていることもあり、手の空いたファクトリーのスタッフで手分けして磨いています」と廣川社長。仕上がった靴にモルトドレッシング用に成分を調整した油性ワックスとスコッチウイスキー「ダルモア」を使って一足につき30分、丁寧に仕上げていく。こうした手仕事がファクトリーにて、ある程度の規模で行われているとは思いもよらなかった。
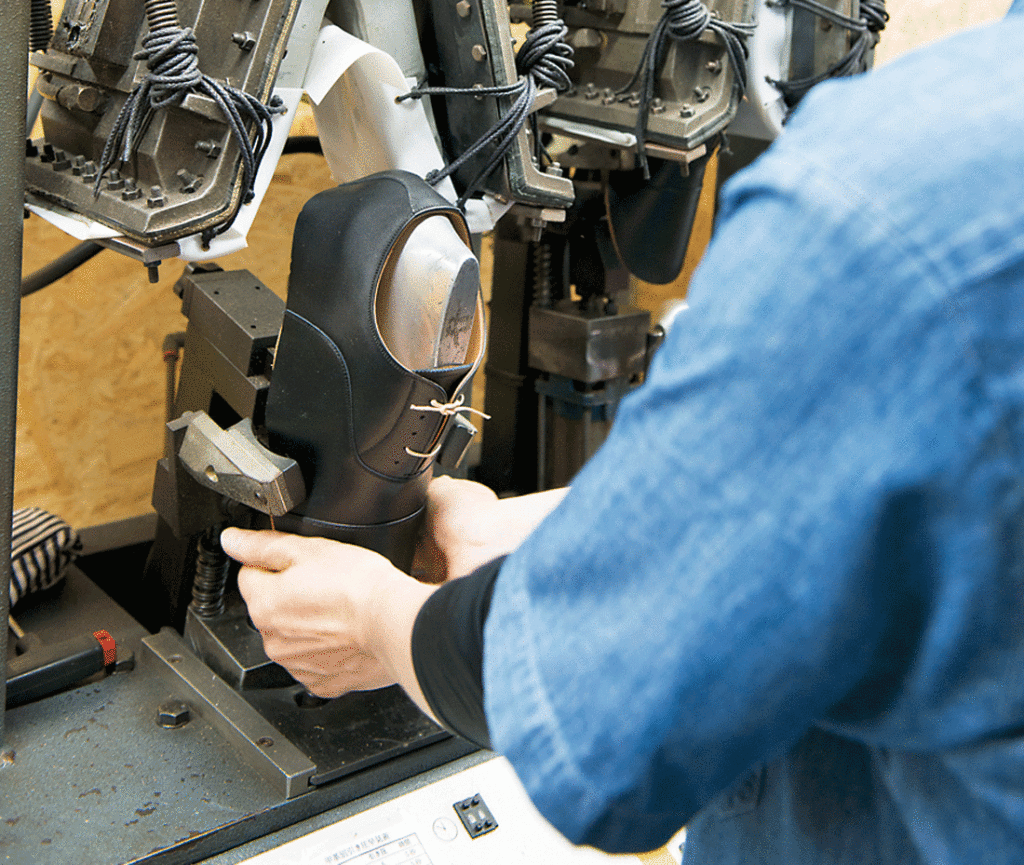
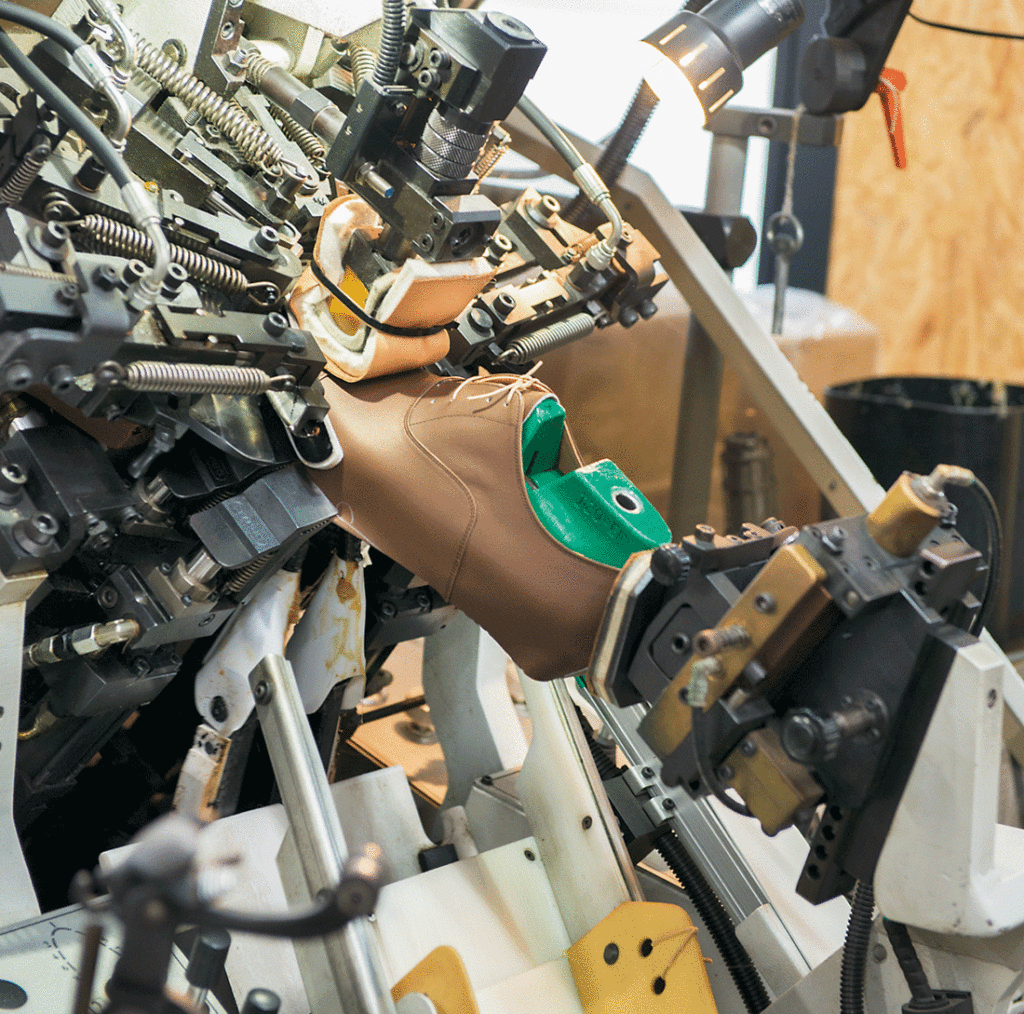
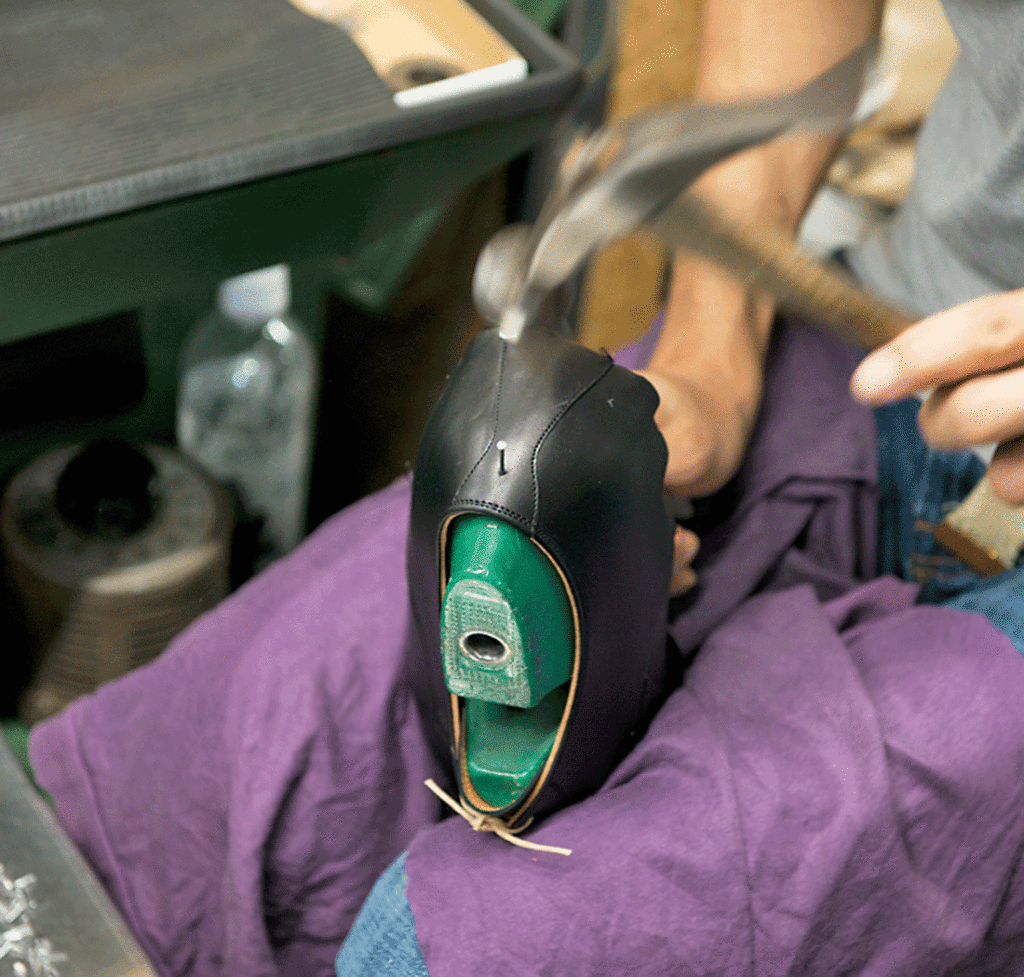
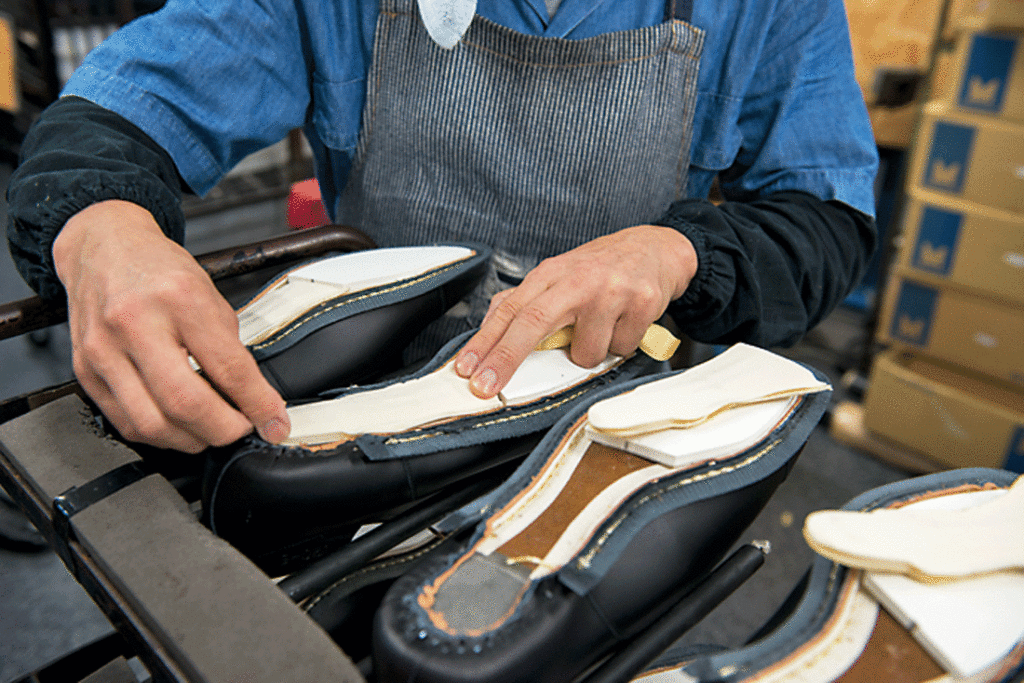
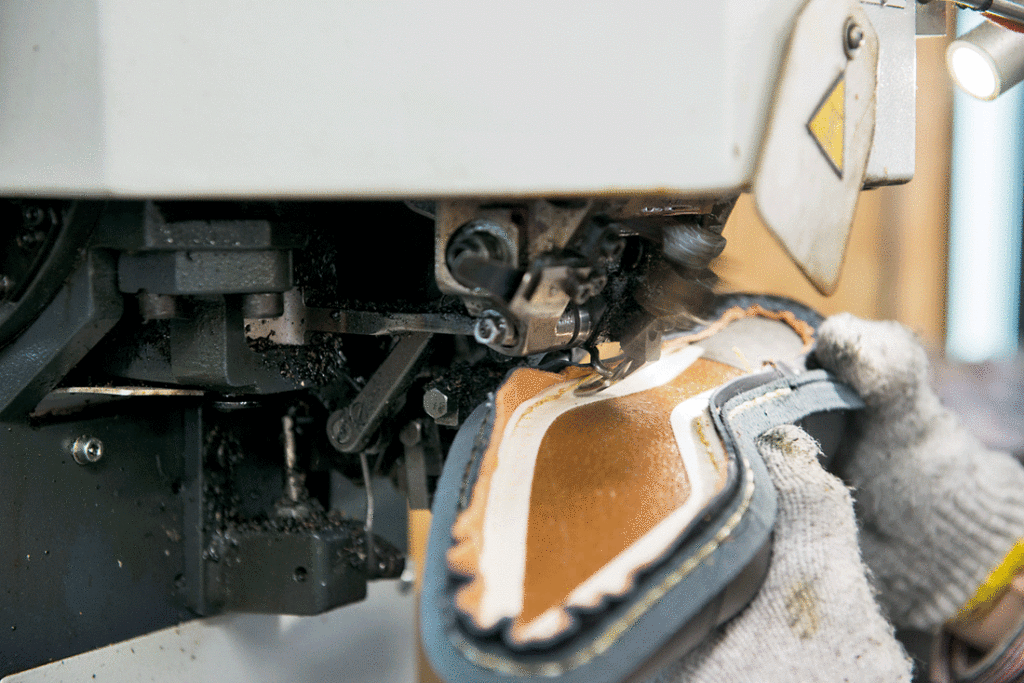
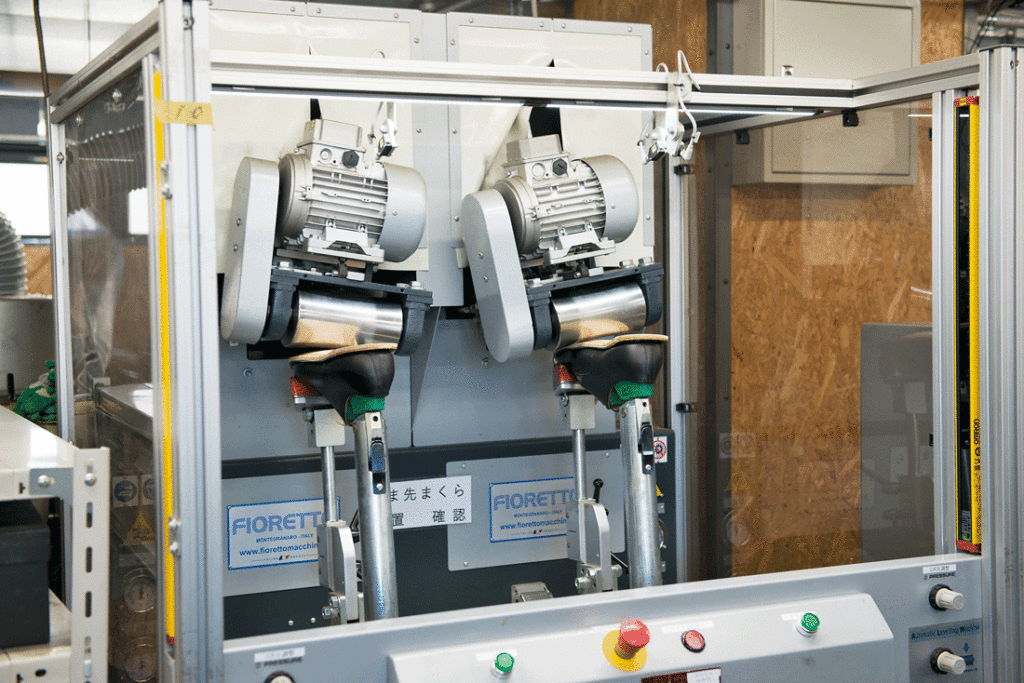
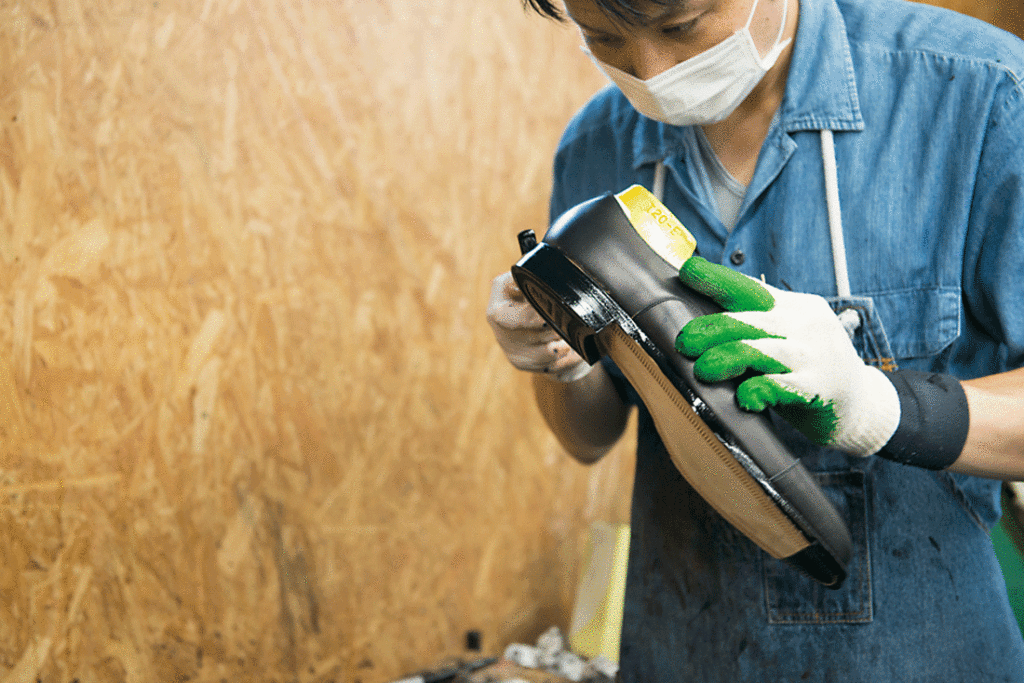
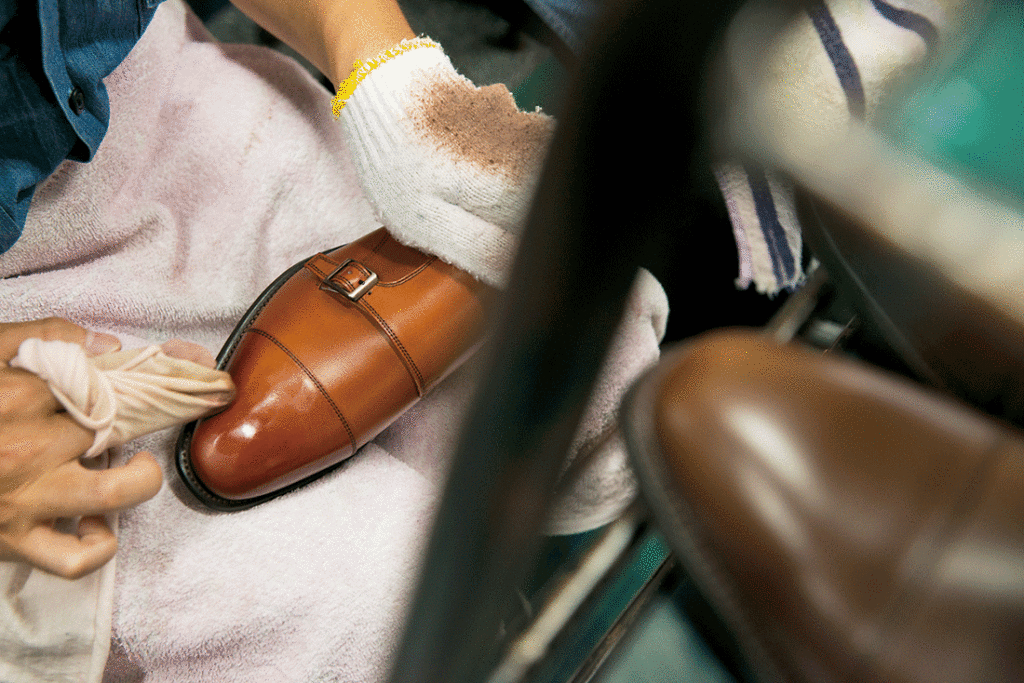
「ちょっとお見せしたいものがあるんです」と、廣川社長は取材班を屋上に案内した。そこには多くのソーラーパネルが配置されていた。「現在ファクトリーの照明の3分の1をこれで賄っています」と廣川社長。最近の新社屋の流行、と冷ややかに見ることもできるかもしれない。ただ、ここまで見てきたファクトリーの様子と、そこに見え隠れするものづくりへのスタンスを感じるにつけ、これもまた『スコッチグレイン』のメーカーシップの発露かもしれないと、妙に納得したのだった。
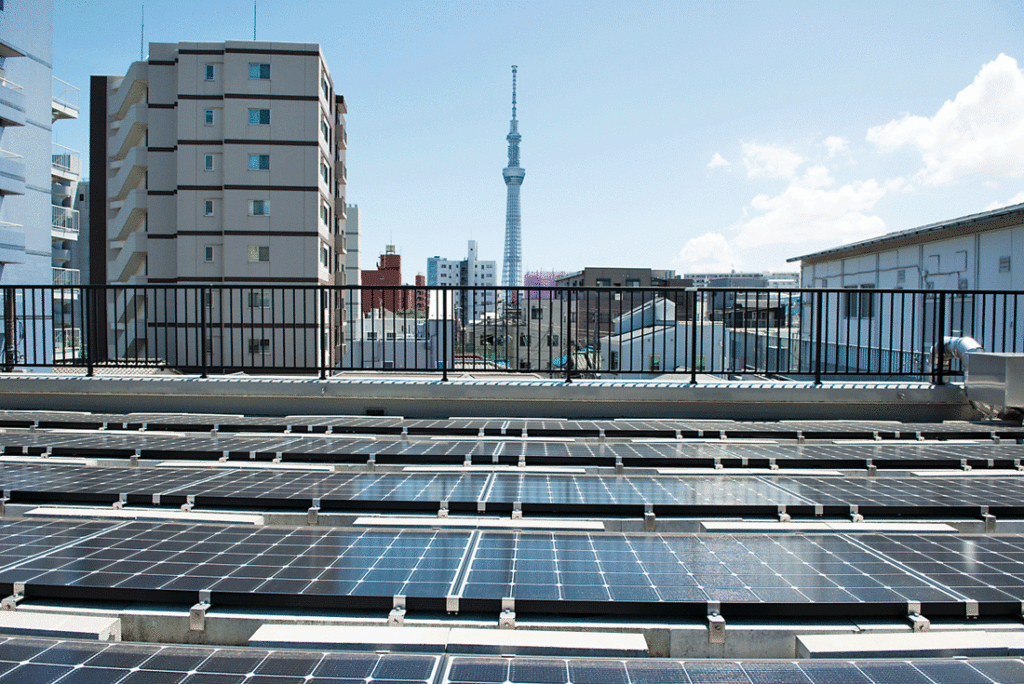
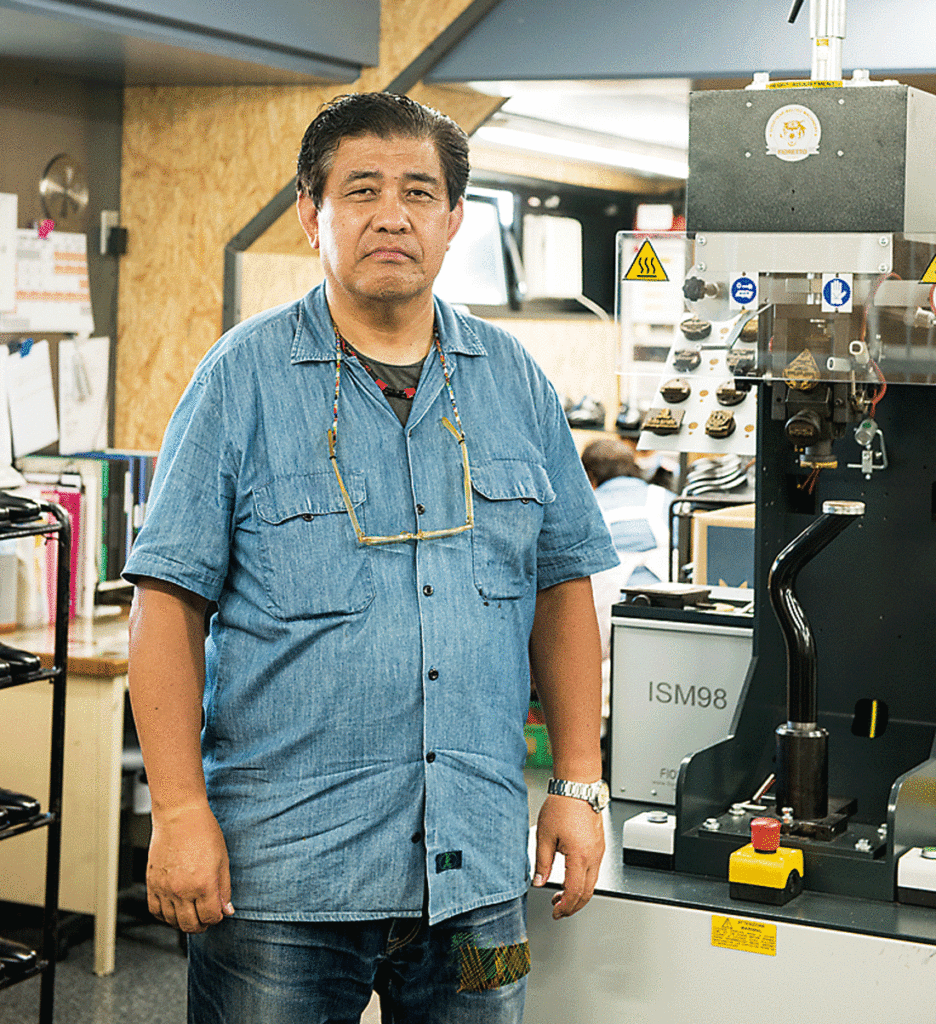
information contact
スコッチグレイン銀座本店
tel:03-3543-4192
photographs_Satoko Imazu
〇 LAST issue21 より